The heat exchanger must meet certain physical requirements both to carry out the specified heat exchange and operate properly as part of a system. As such, it must provide the correct area for the specified heat exchange while maintaining a reasonable pressure drop, contain the pressure of the streams, prevent leaks between the tubes and the shell, account or thermal expansion, allow for cleaning of fouling deposits, allow for thermal expansion, and phase changes in certain applications.
It should be noted that heat exchangers rarely operate at the exact conditions specified for design. Because performance will decrease with fouling, a heat exchanger may be initially overdesigned, and after some amount of fouling, underdesigned, at which point cleaning should take place. Depending on the performance of a heat exchanger at any given time, downstream processes may be affected.
Thermal and hydraulic requirements
A certain amount of energy needs to be exchanged, and the pressure drop across the heat exchanger must be accounted for in the context of the process. It may be acceptable, or may need to be maintained using pumps. The key tradeoff in heat exchangers is the heat exchanged vs. pressure drop. More surface area can always be added, but the pressure drop may become unacceptable for downstream processes. The thermal difference in the two fluids should also be considered in picking the proper heat transfer equipment, as some materials and types of heat exchangers accept larger temperature differences while others are not as efficient.
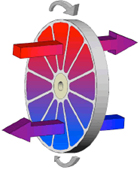
Figure 1: Turbo heat exchanger (process-heating.com)
Material compatibility
Heat exchangers must be able to maintain acceptable performance through prolonged contact in the materials with which heat is being exchanged. While regular maintenance and cleaning is unavoidable, appropriate construction materials should be chosen that are not prone to excessive corrosion or fouling. In addition, there is a certain tradeoff between costs and safety. Materials that are chosen with poor specifications to the given heat transfer application will see leakage, fouling, and possible brittleness (through temperature changes). This will lead to potential loss of material through leaks and even explosions. Material compatability is one of the most important parts in designing a heat exchanger. It is generally worth investing in a quality material that costs more upfront, as maintenance, repair, and cleaning costs will be much cheaper later on, offsetting the higher initial costs.
Operational Maintenance
Fouling on the heat transfer surface will reduce the overall heat transfer coefficient and efficiency. To maintain economical operation, the fouling will need to be periodically removed. Depending on the type of heat exchanger used, it may be disassembled and cleaned, or it will have to remain intact and be cleaned chemically, which can involve hazardous materials. Some heat exchangers are more easily disassembled and cleaned, while others are not. This trait will lead to a significant increase (or decrease) in costs. Depending on the application of the heat exchanger, it may be more vital to constantly check the amount of residue buildup in the exchanger, as this may lead to leakages, malfunctions, or explosions. There should be valves and other process controls that can monitor the current status of the exchanger, which will alert the operator to know when it is time to perform a maintenance checkup.
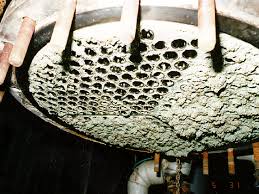
Figure 2: Fouled heat exchanger (regonline.com)
Environmental, health, and safety considerations and regulations
Hazards and toxicity of the streams involved must be guarded against, and safety codes must be met. Plans must be prepared to deal with leaks or failures of the heat exchanger that will minimize adverse effects. Any hazardous waste should be taken care of using proper protocol, and at the very least adhering to the guidelines of the laws in the area. However, ethics do not stop at national borders, so one must be very careful when dealing with toxic waste, especially in a populated area or ecologically rich area. Safety of the operators and workers should always be prioritized, and at no point should anyone be in any danger. If this is the case, then there needs to be a major change in the plant procedure.
Availability and cost
As with any project, the ability of the heat exchanger construction to fall within the deadlines and costs is key to the economics. Each material used to construct the heat exchanger should be properly examined for how it reacts and handles the liquids/gases that will be involved in heat transfer. There is a significant trade off between cost of material and safety. Analysis on what the required specifications in the given heat transfer application is vital to correctly identifying the correct material to use. In addition to the capital fixed costs in obtaining the heat transfer equipment, one should also analyze the variable costs. For example, the cost for the energy required to perform the proper amount of heat transfer as well as the repairing and maintaining costs of the exchanger when there is residue buildup.
Leave a Reply