The purpose of industrial electrolysis is to use electrical energy to convert raw materials into desired products. This conversion of raw materials takes place in an electrochemical reactor. Since energy is added, the electrochemical cells used are electrolytic rather than galvanic. Hence, the term industrial electrolysis is used to describe these processes. Just two electrolytic processes, the production of aluminum and the chlor-alkali process, consume about 90% of the electricity used in all electrolytic processes. These examples merit special attention in this chapter.
An important difference between industrial electrolytic processes and many of the electrochemical processes that we have considered to this point is the use of flow. Industrial processes frequently operate with a continuous flow of reactants and products. Semicontinuous and batch processes are also used. Reaction rates and, in particular, reaction rates per volume are critical, and can frequently be raised by increasing the transport rate of reactants and products to and from the electrodes. A key parameter in the design of electrochemical reactors is the current density, which determines the area needed and, hence, the number and size of cells required to achieve a desired rate of production. Voltage losses in the cell are also important and determine the energy necessary for production, as well as the energy efficiency of the process. Finally, several important processes involve products in the form of evolved gases.
We begin with an example of an industrial electrolytic process—chlorine production by what is known as the chlor-alkali process. The reactant stream for this process is a purified, saturated brine of NaCl, which flows continuously into the reactor. In addition to chlorine, sodium hydroxide and hydrogen gas are produced simultaneously in the reactor. The two electrochemical reactions are


The standard potential for full cell is 2.188 V. Figure 14.1 illustrates a diaphragm cell, which has been the dominant type of chlor-alkali cell used in the United States for many years. A newer membrane cell is replacing the diaphragm cell in applications across the globe and will be discussed later in the chapter. Early diaphragm cells consisted of vertical anodes of graphite, steel mesh cathodes, and an asbestos separator (diaphragm). Chlorine is evolved at the positive electrode (anode) and the brine flowing in the compartment is called the anolyte. At the cathode, hydrogen is evolved and hydroxide ions are produced. The electrolyte is called the catholyte. A diaphragm keeps the product gases from mixing and is an effective barrier for separating the chlorine and hydrogen. Importantly, however, the diaphragm is permeable to the liquid solution, thus allowing for transport of ions between electrodes. Figure 14.2 shows transport in the diaphragm in more detail. In this design, the solution flows from the anode through the diaphragm to the cathode. This flow helps prevent NaOH from back-diffusing into the anode side of the diaphragm. Within the diaphragm, bulk fluid flow, migration, and molecular diffusion are all present. On the cathode side, the catholyte is removed as one of the products, containing NaOH with some chloride ion contamination. The NaOH is recovered in a subsequent process. Assuming that all of the electrical current goes to support the above reactions, a simple material balance can establish the exit composition if the inlet flow rate and cell current are known. Both Cl2 and H2 are removed from the cell as gaseous products. The composition of NaOH at the exit for this type of cell is ∼12 wt%, and the purity of the chlorine gas produced is 98%. Since chloride ions are consumed at the positive electrode (anode) and hydroxyl ions are produced at the negative electrode (cathode), ions must move to balance the charge; that is, there is an electrical current flow in the solution. Ideally, only Na+ would move from anode to the cathode. This best case is not achieved completely with this design; it is important, nonetheless, to minimize the amount of hydroxide ions that reach the anode and the concentration of Cl− ions that enter the cathode chamber. As you have probably already noted, the diaphragm cell illustrates many important aspects of industrial electrolysis.
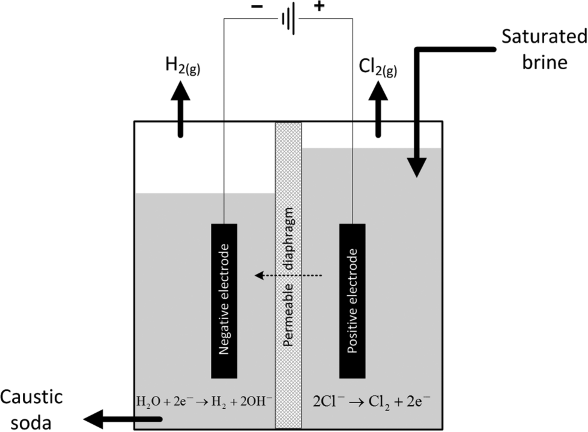
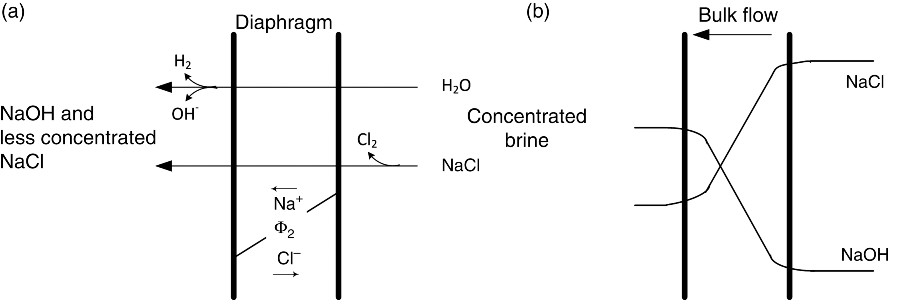
About 44 million metric tons of chlorine are produced annually. Assuming that all of this production takes place in diaphragm cells, we estimate the total power required for this production in Illustration 14.1.
ILLUSTRATION 14.1
Calculate the electrical power needed to produce the global supply of chlorine with diaphragm cells. Use an annual production of 44 million metric tons Cl2 per year. The operating voltage of a diaphragm cell is about 3.45 V, considerably higher than the equilibrium voltage.
- Convert the rate of production to kg·s−1 of chlorine
- Use Faraday’s law and the cell potential, 3.45 V
We next consider several important performance measures for industrial electrochemical reactors.
Leave a Reply