Description of the deposition process rapidly becomes more complex as we move from the isolated nuclei of initial growth to interacting growth sites and, finally, coalescence and layer growth. The fundamental processes described above, however, provide a basis for understanding the deposit morphologies that are observed in practice. They also help us to understand ways in which additives may influence the deposition process as we will see later in this chapter.
The role of the fundamental processes in determining the deposit morphology is a strong function of the surface overpotential and, therefore, current density. In this section, we make some generalizations regarding that relationship. In doing so, we note that there are a number of subtleties not factored into these generalizations that can have an important impact on the morphology and other physical properties of the deposit. For example, growth rate differences or differences in the reaction mechanisms on individual crystal planes can make a huge difference on the size and orientation of crystal grains in the resulting deposit. Also, our generalizations do not explicitly consider the impact of additives in the plating bath, which are discussed later in the chapter.
At low overpotentials, deposition is limited by surface diffusion of adions to preferred sites as there is insufficient energy for nucleation. The adion concentration on the surface is low, as is the concentration gradient for surface diffusion. Growth is primarily at kink sites, and the structure of the imperfect crystal surface is critical in providing those sites. Deposits are almost always polycrystalline, although crystal sizes can be large; crystal structures are well-formed.
As the overpotential is increased, the adion concentration increases and growth may occur at less energetically favorable sites (e.g., step sites). Growth is still crystallographic, and may result in bunched layers and ridges. As the overpotential is increased further, nucleation becomes important and deposit growth is no longer dependent on existing growth sites. As described previously, nucleation increases sharply with overpotential leading to deposits with large numbers of crystal grains because of the additional sites available for deposit growth. Nucleation occurs at multiple sites and the resulting crystallites coalesce to form the deposit. Defects are present in the crystallographic structure of the deposit due to coalescence of the distinct crystallites or grains. The relative rates of nucleation and growth determine the number of crystals and hence the granularity of the deposit. The large number of crystal grains may persist as the deposit continues to grow, leading to a hard, rigid polycrystalline deposit. In contrast, nonuniformities in the growth rate of different crystal planes can result in the formation of larger crystals as the deposit thickens, and may even lead to columnar deposits. Deposits with fewer large grains tend to be more ductile. Coalescence to form a complete layer is typically complete by the time a thickness of about 10 nm has been reached.
Mass transfer of the reactant species to the surface from the bulk eventually becomes important as the overpotential, and hence the rate of the reaction at the surface, continues to increase. Deposit growth under mass-transfer control leads to roughened deposits that are often powdery, and thus, unsatisfactory from a metal finishing perspective. For this reason, electrodeposition is typically performed at only a fraction of the limiting current. Dendritic growth is also possible under mass-transfer limiting conditions where deposition occurs preferentially at protrusions due to higher rates of mass transfer to those locations.
The above generalizations are illustrated in Figure 13.11. As shown, side reactions such as hydrogen evolution also become important as the cathodic overpotential is increased. While the figure shows hydrogen evolution following the mass-transfer plateau, this is certainly not always the case. For example, improvement of mass transfer in the cell due to the addition or increase of convection may raise the mass-transfer limit so that hydrogen evolution occurs prior to reaching that limit. Typical faradaic efficiencies for deposition approach 90%, although some processes, such as chromium deposition, have much lower efficiencies (20% or less). Hydrogen evolution is the principal side reaction that occurs during the electrodeposition of metals from aqueous solutions.
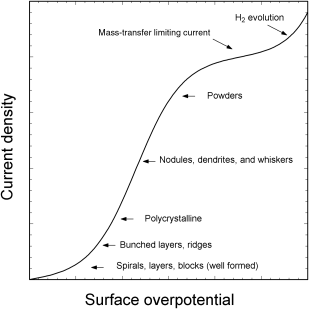
According to Pletcher, industrially electrodeposited layers range, in general, between 0.01 and 100 μm, although most are 1–10 μm thick. Adhesion and mechanical properties are also important so that the best deposits are not necessarily those formed at the lowest current density. For example, the adhesion of small-grained polycrystalline deposits is frequently better than that of large-grained deposits. For electrodeposition, average current densities range from 100 to 1000 A·m−2, although higher rates are possible with some baths. Most electrodeposition is performed with a DC power supply at constant current. Pulse plating, however, is important for special applications, but is beyond the scope of this chapter. Since good quality deposits are formed at current densities well below the mass-transfer limit, convection is an important aspect of electrodeposition cell design. Note that the methods described in Chapter 4 can be used to estimate the mass-transfer limiting current.
Leave a Reply