Let’s now take a more detailed look at the components of a bipolar fuel-cell stack as illustrated in Figure 10.4. Multiple layers are assembled together to form a cell, and these layers are arranged like a deck of cards to form the stack. Starting from the center of the cell in Figure 10.4 and working out, the electrolyte keeps the fuel and oxidant from mixing and also provides for an ionic path between electrodes. You can also think of this as a separator. Key requirements of the electrolyte are high ionic conductivity and low rates of permeation of the reactants. Of course, it must be an electronic insulator to isolate the two electrodes from each other and prevent the cell from being shorted. In addition to high conductivity, a high transference number of the ion that is involved in the electrochemical reaction is desired.
Next are porous electrodes as described in Chapter 5. Most often a catalyst is used to reduce the overpotential at the electrodes, and generally the electrodes for the anode and the cathode are different. Intimate contact of the reactants, electrolyte, and electronic conducting material, as well as the catalyst, is required to achieve the triple-phase boundary discussed in the previous chapter.
The bipolar plates generally will not be mated directly to the electrode surface. There is an additional porous layer between them as illustrated in Figure 10.5. This layer, called a gas-diffusion layer (GDL) in PEMFCs, allows access by the reactants to the entire electrode surface. Without this layer, the lands (also called ribs) would prevent the reactants from easily reaching the area under the ribs. This gas-diffusion layer should be highly porous to permit easy access to the electrode surface by the reactants, but also must be an electronic conductor. These gas diffusion layers are about 200 μm thick.
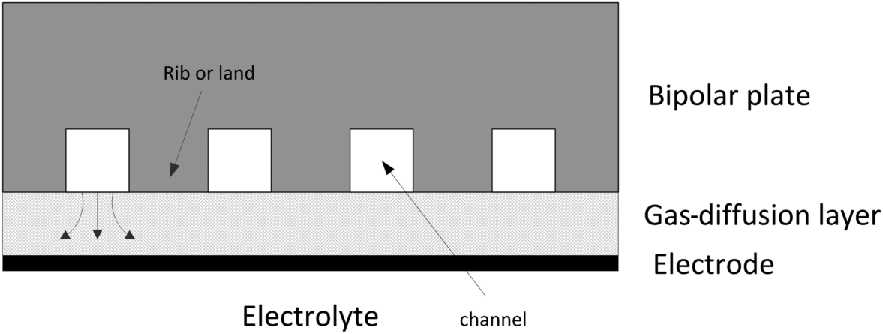
Typically, fuel and oxidant are supplied continuously, and the fuel cell will operate as long as reactants are provided. The fuel and oxidant are distributed with bipolar plates (called interconnects for SOFCs, and sometimes referred to as bipolar separator plates). As mentioned previously, these plates must form a barrier between cells in order to prevent mixing of reactants. Also, in contrast to the separator or electrolyte, the bipolar plate must be a good electronic conductor and have no path for ionic current. Thus, they tend to be dense solid materials. These plates serve to electrically tie the anode of one cell with the cathode of the adjoining cell, forming a series connection.
Analysis of the flow fields will be covered in the next section. Assuming that the thicknesses of the components shown in Figure 10.4 are known, the size of the cell stack can be determined. The calculation is straightforward, and the key metric can be summarized by a quantity called cell pitch. This parameter is simply the number of cells per unit length when the repeating units are stacked together. The thicknesses of the endplates are added to the combined thickness of the repeating units to give the total stack length.
The last quantity we want to introduce is a ratio of active area to planform area. If we examine the planform, we note that a portion of the area is allocated to sealing, and distributing reactants, namely, a manifold. To account for this, we simply use an active area ratio:
(10.17)
The connection between the manifold and the individual cells is illustrated in Figure 10.6; the active area ratio is evident from the top (planform) view. Illustration 10.3 demonstrates the calculation of the fuel-cell volume.
ILLUSTRATION 10.3
If the cell in Illustration 10.2 had a cell pitch of 3 cells cm−1 and the active area ratio is 0.7, calculate the volume of the cell stack. The endplates may be neglected.
The length of the cell stack is

The planform area is

The volume is, therefore,

The actual volume will be larger still because a loading system is needed to apply a force to compress the stack axially, and hardware may be needed to attach the manifolds and to mount the cell stack assembly in the system.
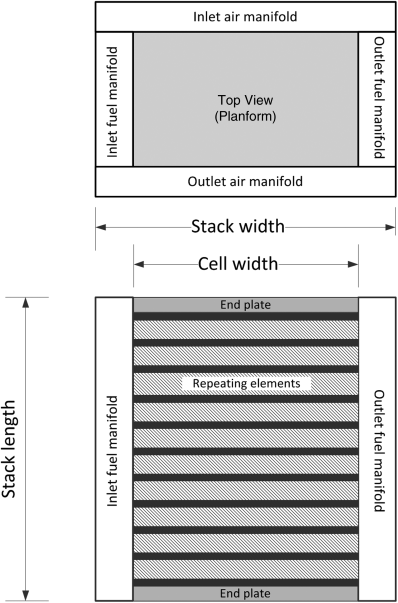
Leave a Reply