To this point in the chapter, we have examined several aspects of cell and battery design. This section takes a brief look at ways in which cells and modules are constructed. The mechanical designs can be complex, and often manufacturers differentiate their products on these attributes.
Almost invariably, it is desirable to have cells and modules in a sealed container. In the case of lithium batteries, for instance, contact of the active materials with water and oxygen must be avoided; thus, a hermetic seal is required. The internal components of some cells can be exposed to the atmosphere, but it is still generally preferable to have a sealed design in order to prevent escape of electrolyte and any gases generated during normal operation. The container or casing is either metal or plastic, depending on the application. Gases can be generated due to normal operation or due to an internal cell failure. Uncontrolled venting of gases as a result of cell faults varies from mild to violent, and depends on the chemistry and size of the cell. Thus, with a sealed casing, a means of safety pressure relief (Figure 8.9a) is needed to avoid injury and equipment damage. The complexity of the pressure relief system depends on the needs of the particular application. Each case must also include a positive and a negative terminal. Any current that enters or leaves the cell or module must pass through the terminals. Terminals come in a wide variety of sizes and shapes, and have features that manifest little uniformity among manufacturers.
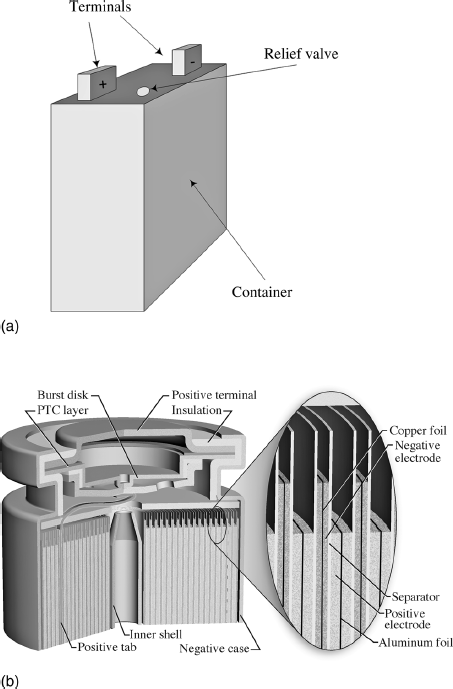
Cells may take many forms. Here we will discuss only the more prevalent types: prismatic, plate designs, cylindrical, and coin. Prismatic cells take the shape of a rectangular prism, or simply a three-dimensional rectangular object with six faces that are rectangles. Because they can pack together efficiently, prismatic cells are preferred where space is limited. One method of forming a prismatic cell is to stack electrodes (plates) together as shown in Figures 8.7. The size and shape of the electrodes can be controlled independently. Multiple cells can also be combined and connected in series to create a battery as shown in Figure 8.8. The details of a prismatic design will depend on the cell chemistry. For instance, both lead–acid and lithium-ion cells can be made in a prismatic form, but the design details are quite different.
The common alkaline cell is cylindrical and probably already familiar to you. Construction starts with a steel can, which also serves at the current collector for the positive electrode. Active material is then molded to the inside wall, a separated introduced, and the negative material and electrolyte added. A metal pin is inserted to collect the current for the negative electrode before sealing the can. An alternative method of creating cylindrical cells is to wind two electrodes around a core. The winding consists of current collectors coated with active material on both sides and two separator layers, as shown in Figure 8.9b. The winding is then inserted into a casing. The capacity of the cell is increased by adding more windings. Although the typical form of a spirally wound cell is a cylinder, prismatic cells can also be made this way.
Coin or button cells (Figure 7.2) are used extensively in research and in many consumer applications. Most often they are used where only a single, small cell is needed. Similar to prismatic cells, they find use where space is limited. In a coin cell, two circular electrodes are separated by a porous material. The cell components are sealed in a coin (button)-shaped metal can, where a gasket is used to prevent the top and bottom of the can from being in electrical contact. In this design, the top and bottom of the can serve as the terminals.
Another important role for cases and packaging is to provide a force to keep battery components in electrical contact and to reduce the redistribution and loss of material during cycling. Although this force is generally not as critical for batteries as it is for the bipolar design used in fuel cells, a means of providing compressive load is often desired and can be essential for some applications and designs. Mechanical issues are considered in more detail in Section 8.10.
Leave a Reply