Synthesis of ammonia from nitrogen and hydrogen is often considered the most important chemical process for mankind, and rightfully so [1]. The element nitrogen is involved in every level of biological function in all living organisms. Despite the inexhaustible reservoir of diatomic molecular nitrogen in the atmosphere, the major limitation to growth of living beings is the availability of elemental nitrogen for basic biochemical processes within a living being, as very few of the living organisms have the ability to fix molecular nitrogen. Bacteria belonging to the family Rhizobia are the most important microorganisms that are able to fix nitrogen by converting it to ammonia at ambient conditions. Growth of agriculture, and hence the food supply, was limited in the past by the availability of such bacteria to replenish the soil nitrogen used by crops. Industrial synthesis of ammonia allowed mankind to overcome this limitation, making it possible to feed and sustain the billions of human beings who now inhabit the earth [2].
For a long time, it was considered impossible to effect a synthetic reaction between nitrogen and hydrogen at a rate that would make the process amenable to commercial exploitation. Several eminent personalities, including Ostwald2 and Nernst,3 conducted detailed investigations without much success. Ultimately, Fritz Haber, a German chemist, demonstrated in his laboratory that it was possible to obtain reasonable yields of ammonia through the use of iron-nickel catalyst [3]. This discovery earned Haber the Nobel Prize in Chemistry in 1918.4 The commercialization of the reaction for bulk production of ammonia was accomplished with the involvement of Carl Bosch, leading to the Haber-Bosch process, which is the foundation for fertilizer production worldwide. Bosch was awarded the Nobel Prize in Chemistry in 1931 (along with Friedrich Bergius) for his pioneering work in high-pressure chemistry [4].
2. Wilhelm Ostwald received the Nobel Prize in Chemistry in 1909 for contributions in the fields of catalysis, equilibrium, and kinetics.
3. Walther Nernst received the Nobel Prize in Chemistry in 1920 for contributions in the fields of thermodynamics and electrochemistry.
4. An unintended and unfortunate consequence of this ability to synthesize ammonia was that Germany was able to synthesize ammonium nitrate needed for explosives and ammunition, a development that prolonged World War I (Max Perutz, I Wish I Had Made You Angry Earlier, Essays on Science, Scientists and Humanity, Cold Spring Harbor Laboratory Press, Cold Spring Harbor, New York, 2003).
An abbreviated flowsheet5 of the ammonia production process is shown in Figure 3.1 [5]. Nitrogen-hydrogen mixture is fed continuously to the ammonia converter, which is a catalytic reactor where the ammonia synthesis reaction takes place. The product stream consisting of ammonia and unreacted reactants is continually withdrawn from the reactor. This product stream exiting the reactor is not useful in its form, as the subsequent ammonia-based processes (nitric acid and fertilizer production, etc.) require pure ammonia. Further, the unreacted reactants are also valuable and need to be recovered. The product separations section accomplishes both the objectives—yielding pure ammonia product, and recovering the unreacted reactants for recycling to the reactor.
5. A flowsheet is a schematic representation of the process, showing various pieces of equipment used in the process and the material flows in and out of these pieces of equipment.
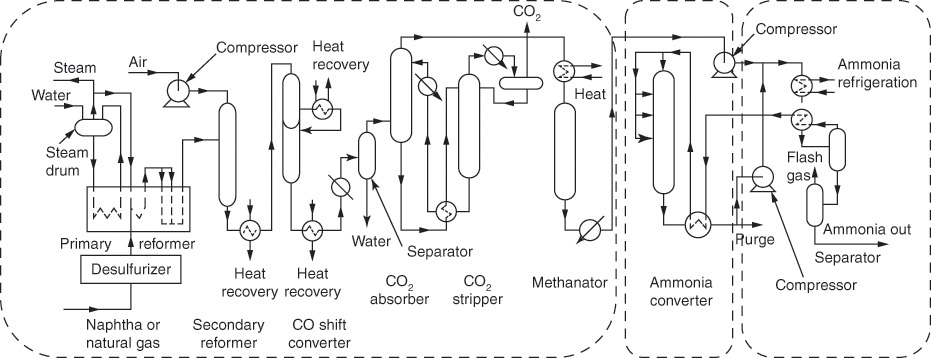
Figure 3.1 Ammonia synthesis process plant.
Source: Austin, G. F., Shreve’s Chemical Process Industries, Fifth Edition, McGraw-Hill, New York, 1984.
Just as processes utilizing ammonia require pure ammonia, the ammonia synthesis reaction requires pure nitrogen and hydrogen reactants. The processes shown upstream of the ammonia converter are required for just this purpose. Neither nitrogen nor hydrogen, while abundant, occurs naturally in pure form. Nitrogen is present as a molecular species, but mixed with oxygen in air. Hydrogen is inevitably found in a bound form—in compounds with oxygen and carbon. The predominant process for obtaining hydrogen is steam reforming of hydrocarbons (primarily methane). Essentially, carbon-hydrogen bonds in the hydrocarbon are cleaved by forming carbon monoxide and then carbon dioxide. The energy required for the process is obtained by the combustion of the hydrocarbon. Oxygen needed for the combustion is obtained from air, consumption of which generates nitrogen. Further separations are conducted to remove all other components, ultimately yielding the desired reactant stream, which can be fed to the ammonia converter.
The various processes and operations conducted in the ammonia plant can be grouped into three blocks, as shown in the figure: raw material processing, ammonia reaction, and product separation. The ammonia converter—the reactor—is the heart of the process. However, several other operations play equally vital roles to make the process functional. As can be seen from this flowsheet, the reactor itself is only a small component in the overall process. This observation related to ammonia synthesis can be extended to practically any chemical process plant. A generalized block flowsheet (where any processing step is represented by a block rather than the representative equipment symbol) for a typical chemical process is shown in Figure 3.2 [6].
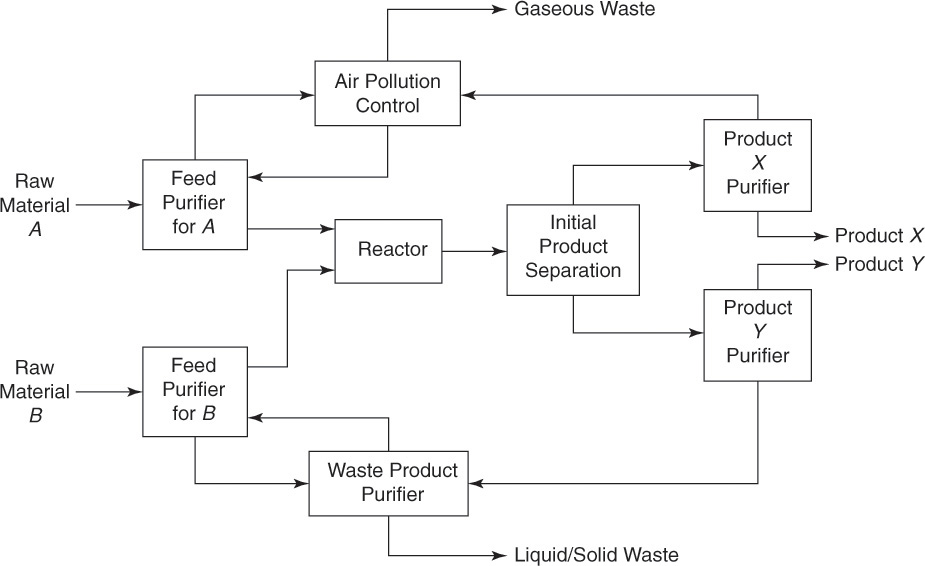
Figure 3.2 Generalized block flowsheet of a chemical process plant.
Source: Luyben, W. L., and L. A. Wenzel, Chemical Process Analysis: Mass and Energy Balances, Prentice Hall, Englewood Cliffs, New Jersey, 1988.
The process is based on the reaction between species A and B to obtain X and Y as the products. The material input to the plant consists of raw materials containing the reactants A and B. Depending on the composition of the raw material (with respect to the reactants), there will be a sequence of operations to obtain the acceptable level of purity in the feed stream to the reactor. As seen from the figure, typically a separate sequence of purification steps processes each raw material stream, yielding a pure reactant that is fed to the reactor. The reactants of desired purity are fed to the reactor and subjected to appropriate processing conditions—temperature, pressure, reaction time, and so on—to be converted into the products. A desired reaction is invariably accompanied by a number of side reactions. Further, some fraction of the reactants is almost always left over in the reactions. The reactor outlet stream—the raw product stream—consists of the desired products, unconverted reactants, and products resulting from the side reactions. This raw product stream is then subjected to another sequence of operations to separate the product streams. If the raw product stream contains significant quantities of unconverted reactants, those may be separated and recycled back to the reaction stage. Streams devoid of any commercial value are discharged to the environment after proper treatment to ensure compliance with the relevant environmental regulations put in place for the protection of human health and environment.
An individual employed as a chemical engineer in such a process should be able to handle responsibilities associated with each step in the process. He/she should have sufficient knowledge to tackle challenges to ensure smooth operation of the plant from the beginning of the raw material processing to final product formulation and disposition of waste streams. These functions and responsibilities, based on the various technical aspects of materials processing, are described in the following section.
Leave a Reply