In the previous section, we examined ways to increase cell capacity in order to decrease the number of cells required in a battery pack. In this section, we examine the impact of cell design on the rate capability or power of a cell. For a given cell capacity, the current and current density are inversely proportional to the time of discharge, which is a key parameter for our discussion in this section:
(8.15)
Thus, long discharge times correspond to low-rate capability, and short discharge times denote high-rate capability. We’ll explore the impact of discharge time on electrode design through a lead–acid cell example. Before doing that, it may be useful to describe qualitatively the process that will be followed in the example. We begin with a cell that is designed for high capacity rather than high rate. We then scale the capacity of that cell down to the capacity that we need for a high-rate application (starting your car). That scaling is done according to the principles of the previous section where the idea is to keep the electrochemical characteristics constant while changing capacity. Therefore, the scaled cell is still designed for capacity rather than rate. Finally, we examine how to modify the cell, keeping the capacity constant, in order to improve the rate performance.
The lead–acid chemistry is almost universally used to start the automotive engine. Colloquially, it is called a SLI (starting–lighting–ignition) battery. High power is needed, but only for a short period of time; the total capacity is less important. Under normal operation, the state-of-charge of an SLI battery does not change substantially. SLI batteries typically have a capacity of about 60 A·h. Other designs of lead–acid batteries are used for back-up power where they deliver power over much longer periods (on the order of hours or tens of hours). In contrast to SLI applications, batteries for backup power applications undergo a large change in SOC during routine operation, operate at a lower specific power, and have a substantially higher capacity. Often these types of cells are referred to as high-capacity or deep-cycle cells. How are the designs of the SLI and deep-cycle cells different? To answer this question, our approach will be to start with a deep-cycle lead–acid cell and then to discuss changes needed to create a SLI cell. The procedure was described above and results are found in Table 8.2, where the bolded numbers represent SLI specifications.
Table 8.2 Design Parameters for SLI and Deep-Cycle Cells
Feature | Existing deep-cycle cell | Deep-cycle cell scaled for SLI capacity | Desired SLI cell |
Nominal voltage [V] | 2 | 2 | 2 |
Capacity [A·h] | 1700 | 60 | 60 |
Discharge time | 10 hours | 30 seconds | 30 seconds |
Cold cranking amps | NA | 71 | 560 |
Mass [kg] | 125 | 4 | 16 |
Internal resistance [mΩ] | 0.4 | 11.3 | 1.4 |
Cycle life | 500 (50% SOC) | 2000 (3% SOC) | |
Quantities in bold are fixed for the SLI cell. |
First, we scale the existing deep-cycle cell from its capacity (1700 A·h) to the desired capacity (60 A·h) of the SLI battery using the cell area. In other words, we decrease the cell area in proportion to the capacity. The internal resistance scales approximately as,
(8.16)
The resistance increases with decreasing cell area since a higher voltage drop is required to drive the same current in the smaller cell. We further assume that the mass of the cell will scale directly with the capacity or area.
(8.17)
SLI batteries are rated in cold-cranking amps (CCA). SAE J537 (Society of Automotive Engineers publication) specifies that this value is the maximum current that can be sustained for 30 seconds at −18 °C without having the voltage drop below 7.2 V (this assumes a nominal 12 V battery that consists of six cells in series); the corresponding voltage for a single cell is 1.2 V. We would like to estimate the CCA for the scaled cell and compare it to the SLI specification. To do this, we use the following equation:
(8.18)
which neglects the effect of temperature. Using the calculated value for the internal resistance of our scaled cell, we estimate the current corresponding to the CCA as 71 A. This current is about eight times lower than the required value of 560 A. Clearly, simple scaling of the deep-cycle cell to the desired SLI capacity will not meet the performance requirements for the SLI battery. Consequently, the electrode design must be changed in order to lower the resistance and increase the power. In doing so, we do not need to nor want to increase the capacity of the battery.
A strategy for increasing the power at constant capacity is to make the individual electrodes or plates thinner as illustrated in Figure 8.8. The amount of active material is the same, but we have used many more (thinner) plates in the SLI design. This strategy does two important things that both increase the rate capability of the cell. First, the electrode thickness is reduced, making it easier to access the available active material. Second, the cell area is increased, leading to a lower current density for a given battery current. Ignoring the benefits of the thinner electrodes for a moment, we can estimate the cell area that is needed to adequately lower the internal resistance.
(8.19)
An internal resistance of 1.4 mΩ is calculated; therefore, the cell area must be increased by a factor of about 8 (11.3/1.4). Thus, to achieve the desired power, the separator area for the SLI battery would need to be about eight times that of the deep-cycle battery, which would result in electrodes that are approximately eight times thinner. In practice, the electrodes are designed to be thinner and also more porous to further reduce the resistance. Thus, the rate performance benefit is significantly greater than that due to just the increased area.
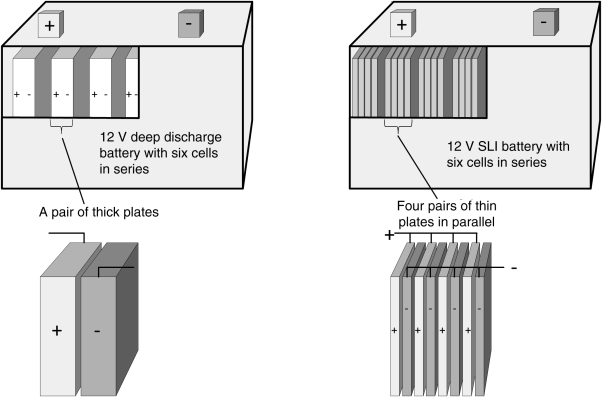
What about the specific capacity? If we discharged the SLI battery at a rate comparable to that of the deep cycle (C/10), would it have a similar specific capacity? The rudimentary analysis just presented suggests that the specific capacities would be the same. However, for each plate, a current collector is needed, and additional separator area is required. When we account for this additional mass, the specific capacity of the SLI cell is lower. More important than the specific capacity is the cycle life. SLI batteries perform very well at the limited DOD for which they are designed. However, while the details are beyond the scope of this chapter, commercial SLI batteries show rapid degradation and a short lifetime when cycled over a large SOC window.
Leave a Reply