A chemical engineer performs a number of different tasks in the chemical industry or an organization engaged in chemical business. The tasks and responsibilities of the chemical engineer that are described in this section are based on the concept of engineering as the transformation process from science to technology.
Consider the case of manufacturing a new chemical product or a new manufacturing process for an existing chemical product. Going from conceptualization to commercial operation is an extremely complex and involved process, and any such undertaking typically moves through the following stages [14]:
1. Conceptualization and inception
2. Preliminary economic evaluation
3. Development of data needed for final design
4. Final economic evaluation
5. Detailed design
6. Procurement and construction
7. Start-up and trial runs
8. Production
A simplified flowchart for the various stages of a typical project are shown in Figure 1.7.
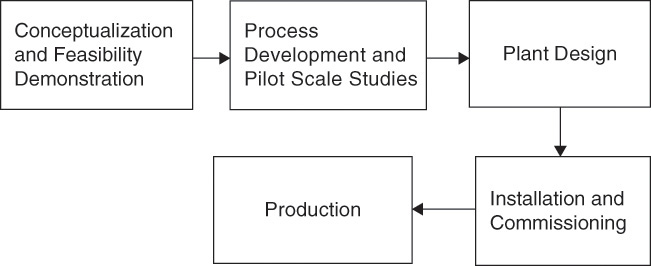
Figure 1.7 Engineering a chemical plant.
The first stage in this development consists of conceptualization of the idea for the new product or process, based on existing technical literature. Before an organization commits financial and other resources to any new venture, it conducts a preliminary economic analysis to gauge the economic viability of the venture. If the venture is judged to be economically attractive, the organization proceeds to the next stage: gathering the necessary information. Extensive laboratory experimentation is generally conducted to demonstrate the feasibility of the idea on the bench scale. Subsequent investigations are conducted over larger scales to ensure repeatable and reproducible results. An integrated process is developed for commercialization identifying the raw materials and processing steps, including those necessary for the treatment of effluents.
The key step, or possibly the entire process, is operated at pilot level to confirm the feasibility. The organization typically conducts a refined, accurate economic analysis using the gathered data. If the project is still commercially attractive, a full-scale plant is designed using scientific and engineering principles and experimental data. The necessary equipment is fabricated and procured from vendors and installed, and the plant is commissioned. Modifications and fine-tuning of processes and operations is invariably required before the plant starts operating consistently, producing the desired product commercially.
A chemical engineer is involved in all of these activities. Depending on his/her responsibilities, the role of the engineer may include one or a combination of the following:
• Research and development engineer: An engineer who is involved in the initial stages of the diagram shown in Figure 1.7 is called a research and development (R&D) engineer. The research component of the position typically involves working with a chemist to investigate the key concept at the bench scale. The development component involves conceptualization of the process based on the key step. The engineer is responsible for identifying the sequence of upstream and downstream processing steps, evaluating alternatives, and conducting investigations on larger scales. Depending on the organization and the complexity of the process, an engineer may be engaged only in research, may conduct only developmental work, or may do both. The R&D engineer designs and executes experimental work, supervises staff, coordinates the data collection and analysis, and handles knowledge interchange among the members of the project team, including the chemist and engineering team. The R&D engineer is essentially the subject matter expert in the team, developing solutions to various challenges. A graduate degree (preferably Ph.D.) is highly desirable for an individual functioning as an R&D engineer.
• Pilot plant engineer: The laboratory investigations typically yield only a few grams of product, while the commercial process may be required to produce thousands of tons of product per day. The laboratory process thus has to be scaled by several orders of magnitude. Before the construction of a full-scale plant is initiated, requiring substantial financial investment, the entire process is inevitably tested in pilot plants having a capacity one or two orders of magnitude lower than that of the full-scale plant. These pilot plants serve two primary purposes: first, they provide validation of the plant design and confirmation of the ability of the organization to successfully operate the process on a large scale; second, they help identify the challenges that arise with the scale-up of the process. For example, heating or cooling of material is generally not an issue on bench scale, but effective energy transfer can become a challenge on a larger scale. Similarly, whereas separation of solids by filtration can be a straightforward matter in the laboratory, it can limit the process efficiency and prove to be a bottleneck when scaled up. The pilot plant operation provides information about such potential technical problems and provides an opportunity to devise and test workable solutions to these problems. Pilot plant engineers run these plants, discovering potential problems, and devising, testing, and perfecting solutions to these problems before they manifest in the production plant.
• Design engineer: Sizing of the process equipment and specifying the operational conditions for the process are among the responsibilities of the design engineer. A design engineer, in the chemical engineering field, is mostly a process design engineer4 who performs detailed calculations of energy and material flows, specifies equipment capacities, and determines the layout of the plant. The design engineer interfaces with the R&D and pilot plant engineers to obtain data and information and interfaces with vendors and fabricators to finalize process equipment specifications. He/she also typically develops cost estimates for the process. The tasks of fabrication of equipment, infrastructure development, and installations are typically executed by mechanical, civil, and electrical engineers. The design engineer interacts with these engineers and suppliers to ensure that the installed plant conforms to the design specifications.
4. In other fields, a design engineer may be a product design engineer, one who creates different product designs, such as a new phone or an app.
• Start-up, or commissioning, engineer: The engineer involved in the initial start-up of a new plant is the start-up/commissioning engineer. He/she has the responsibility to ensure that various process units function as designed and the plant is able to deliver the product having the specified purity and quality at the rated design capacity. Once the initial problems are sorted out and the plant is operating smoothly, the commissioning engineer hands over the responsibility to the production operating personnel.
• Manufacturing/production engineer: A manufacturing/production engineer provides support to the manufacturing operation, monitoring daily operations to ensure that operations conform to the process design. He/she investigates process deviations, troubleshoots problems, and continually explores opportunities to increase profitability through capacity enhancement, efficiency improvements, and cost minimizations. The manufacturing/production engineer is responsible for plant safety, product quality and reliability, and costs for operations under his/her charge. Additionally, the manufacturing/production engineer works collaboratively with operations, engineering, maintenance, quality, and other departments to ensure plant reliability and production goals are met. Some plants may employ individuals other than chemical engineers to oversee the operation of the plant and its production. In this case, they may have a chemical engineer associated with the plant; such plant engineers are responsible for improving the productivity of the process, optimizing operations, and troubleshooting any problems that affect the operation of the plant. A facility may have a number of engineers who respond to such issues, and they may be called technical services engineers. All process plants also employ maintenance engineers, who ensure continuity of operation of various pieces of equipment through routine maintenance and repair of broken equipment. These engineers are typically mechanical or electrical engineers, and the production, plant, and technical services engineers interact closely with them.
Smaller organizations or simple processes may not require distinct personnel to perform the different jobs described. The same individual may perform multiple tasks, bearing the responsibility from laboratory investigations through commissioning. Conversely, larger organizations or complex processes may have separate and multiple individuals for each step. Commercialization of the process is always a team task, with the R&D engineer, pilot plant engineer, design engineer, and commissioning engineer exchanging information and refining/optimizing the process. An organization may also outsource many of the activities, contracting R&D with one entity, getting designs from specialist firms, and having plants commissioned by yet another entity.
Apart from these process- and plant-related jobs, many chemical engineers may work as sales or marketing engineers. Many companies need services of an individual to market their products, services, and equipment to other industries. This individual must have a thorough engineering understanding of the particular product/service being offered and is typically called a sales engineer, technical sales engineer, marketing engineer, or a variation thereof. A sales engineer must possess the necessary technical competence and must have excellent communication skills, a desire to interact with people, an ability to understand the client needs, and the ability to work closely with the team to develop products and services in response to these needs. Ability to cultivate relationships is an absolutely essential skill for such positions. A sales engineer invariably spends a considerable amount of time traveling, visiting clients in a territory typically assigned to him/her, and developing a customer base for the company.
Despite the different nature of responsibilities, all the engineering positions may be designated simply as process engineers, which is the most common title for the jobs advertised across the chemical industry. The next section describes briefly the various industries and other sectors of the economy that employ chemical engineers.
Leave a Reply