Most process plants operate in continuous, steady-state mode. Maintaining the plant conditions at the specified design values is essential for meeting the product specifications. At the same time, no processing step is immune from experiencing disturbances due to variations in the quality of raw material streams, malfunctioning of units (pump failure, loss of electrical power, etc.), inlet flow rate fluctuations, and many other factors. A chemical engineer must understand the impact of such disturbances on the output of the process and be able to devise and implement corrective measures to control the process within the accepted tolerance of the setpoint of the process. The course on process control is aimed at equipping students with the knowledge of principles and techniques of process control.
Controlling a process requires understanding the stimulus-response behavior of the process unit. The student learns to develop transfer functions—quantitative descriptions of the change in the process output due to a change in input conditions—for the process unit. Controlling the process requires modification of this transfer function by addition of a control element in the process. This control element enables the plant operator to manipulate a variable to maintain the controlled variable at the desired operation point. This principle of process control is explained qualitatively through the following example.
Consider a holding tank that has a continuous inflow and an outflow of a liquid stream. It is required to control the liquid level in the tank at a set value. It is clear that any variation in the inlet stream flow rate, if not controlled, will cause the liquid level to change. When the inlet flow increases, the control strategy should result in increased outflow. The opposite must occur when the inlet flow decreases. This can be accomplished by installing in the outlet line a valve that can be opened or closed on the basis of the disturbance. The tank level is the controlled variable, the desired level is the setpoint, and the outlet flow (more accurately, the valve position) is the manipulated variable. The control scheme is shown in Figure 3.11 [10].
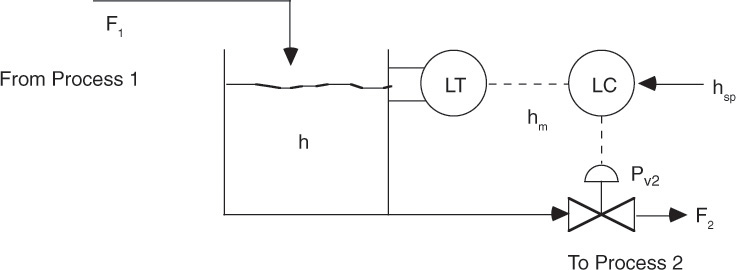
Figure 3.11 Controlling liquid level in a process tank.
Source: Bequette, B. W., Process Control: Modeling, Design and Simulation, Prentice Hall, Upper Saddle River, New Jersey, 2003.
The transfer function for the process describing the relationship between the controlled variable and the feed (inlet flow) is developed, and the desired change in the manipulated variable is quantified on the basis of this transfer function. The process is monitored by making certain measurements. The measured variable may or may not be the same as the controlled variable. In this case, the liquid level or inlet flow rate may serve as the measured variable. It can be seen that several alternative strategies are possible for controlling the liquid level. It may be possible to manipulate the inlet flow rate by installing a control valve in the inlet line, installing an overflow weir, or adding a make-up stream to the system. The process unit downstream of the holding tank may require a set flow to operate, and in this case, the outlet flow rate cannot be a manipulated variable, so an alternative strategy needs to be devised. Temperature, pressure, and concentration are among the other variables that are frequently controlled in chemical processes. Figure 3.12 shows a control scheme for maintaining the temperature of a reactor at the desired setpoint by manipulating the flow rate of the heat transfer medium in the reactor jacket.
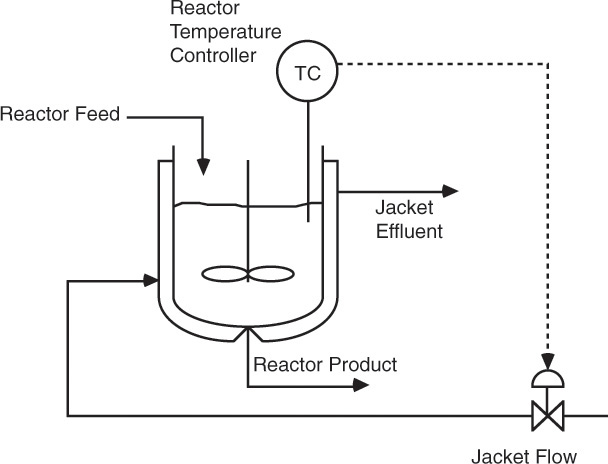
Figure 3.12 Temperature control for a reactor.
Source: Bequette, B. W., Process Control: Modeling, Design and Simulation, Prentice Hall, Upper Saddle River, New Jersey, 2003.
In all cases, the approach for process control is the same: develop the transfer function to quantify the relationships, and design an algorithm to change the manipulated variable to counteract the disturbance. Controlling batch processes involves additional complexity of time dependency. Here the setpoint (the desired value of the controlled variable) may change with time, unlike the continuous processes. Despite this complication, a control algorithm and the control strategy can be developed along the same lines.
Leave a Reply