The United States occupies the top position among chemical manufacturers, accounting for nearly one-fifth of the chemicals produced worldwide [5]. The total value of the chemical goods produced in the United States in 2010 was $701 billion, and the chemical manufacturing sector contributed the largest fraction to the U.S. exports. Table 2.4 shows the 2010 production volumes of some of the important chemicals [6].
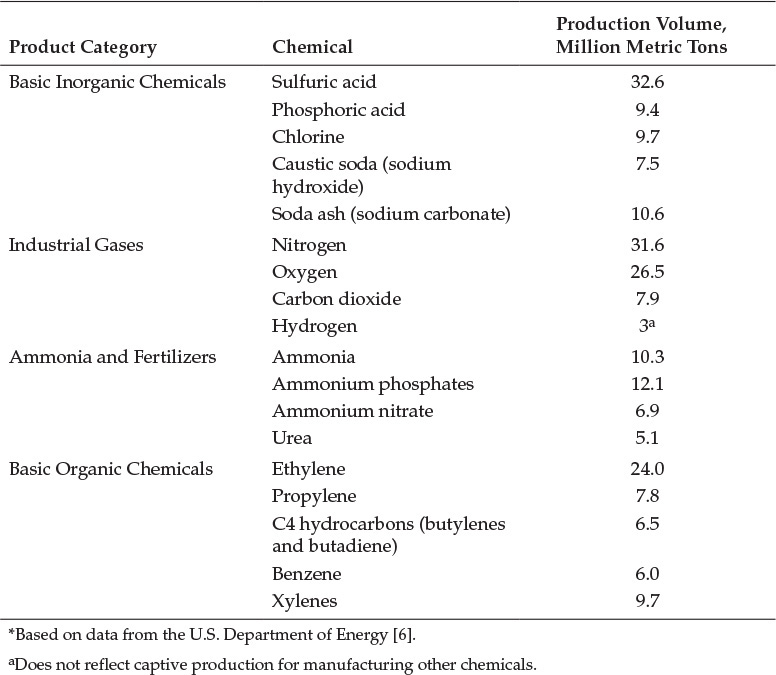
Table 2.4 2010 Production Volumes of Important Chemicals*
The following subsections provide an overview of the manufacturing technologies for some of these important chemicals and their applications.
2.5.1 Sulfuric Acid
Sulfuric acid is by far the largest-volume chemical produced by the chemical industry, and sulfuric acid production is an excellent indicator of a nation’s economy. The U.S. annual production of sulfuric acid is ~36 million tons [5]. The contact process for the manufacture of sulfuric acid involves catalytic oxidation of sulfur dioxide and is a classic example of a chemical process [2]. Figure 2.5 shows a simplified process flow diagram for the contact process. Molten sulfur is fed to the sulfur burner where it is converted to sulfur dioxide by burning it with air. The key step in the process is the conversion of the sulfur dioxide to sulfur trioxide, a reaction that can be carried out economically by using a cheap vanadium pentoxide (V2O5) catalyst.
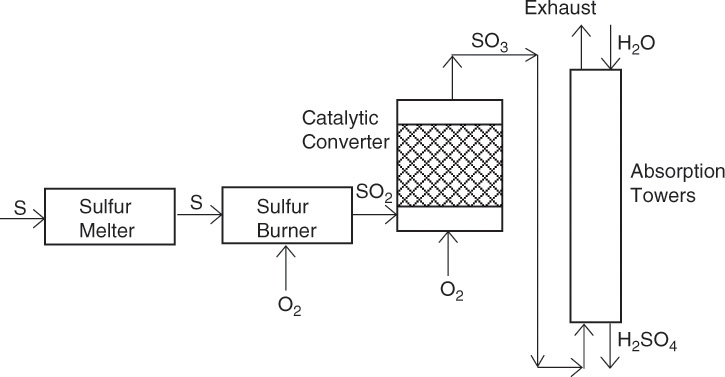
Figure 2.5 Sulfuric acid manufacture process flowsheet.
The design of the catalytic reactor for conducting this reaction represents a classical application of chemical engineering principles. Absorption of sulfur trioxide in water yields sulfuric acid; however, the absorption towers are operated such that the sulfur trioxide exiting the catalytic reactor is first contacted with highly concentrated (>98%) sulfuric acid rather than water. Direct absorption of sulfur trioxide in water is ineffectual, as contacting sulfur trioxide with water results in the formation of acid mist [2]. Typically, two absorption towers are used in most processes; this is known as the double contact double absorption (DCDA) process.
Sulfur, raw material for the process, used to be obtained from sulfur mines and sulfur-bearing porous limestone. At the present time, sulfur associated with fossil resources (sour crude oil, high sulfur coal) as well as pyrite ores supply the sulfur demand for sulfuric acid. A very large percentage of sulfuric acid produced is used in the manufacture of phosphate fertilizers, with other uses consisting of manufacture of a variety of chemicals, petroleum purification, and metal pickling [1].
2.5.2 Caustic Soda and Chlorine
Electrolysis of brine (sodium chloride solution) yields two inorganic chemicals that are major outputs of the chloralkali industries: caustic soda (sodium hydroxide) and chlorine [2]. The manufacturing process for these two chemicals is one of the few examples of application of electrical energy for producing a major chemical product, aluminum production being the other one. An electrolysis process involves coupled oxidation and reduction reactions; in this process the chloride ion is oxidized into elemental chlorine gas, which is accompanied by the reduction (and concomitant splitting) of water yielding the hydroxide ion. Hydrogen gas is also evolved in the process. Two different types of electrolytic cells are used for the process: diaphragm or membrane cells, in which the reduction and oxidation chambers are separated by a barrier, and mercury cells, in which two distinct compartments are used to effect the conversion. Figures 2.6 and 2.7 show the schematics of both the diaphragm/membrane and mercury cells, respectively, with the constitutive reactions shown.
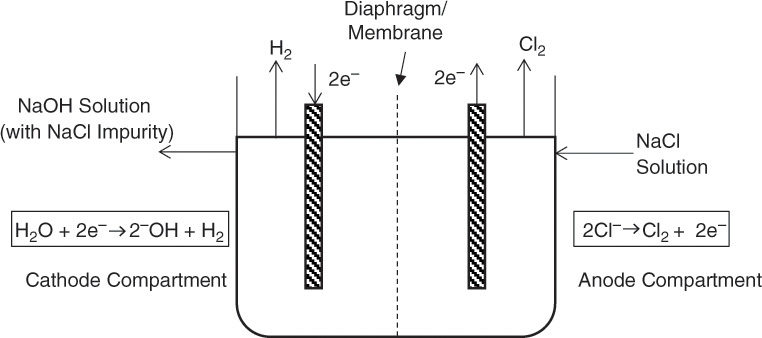
Figure 2.6 Schematic representation of diaphragm/membrane cell used in chloralkali industry.
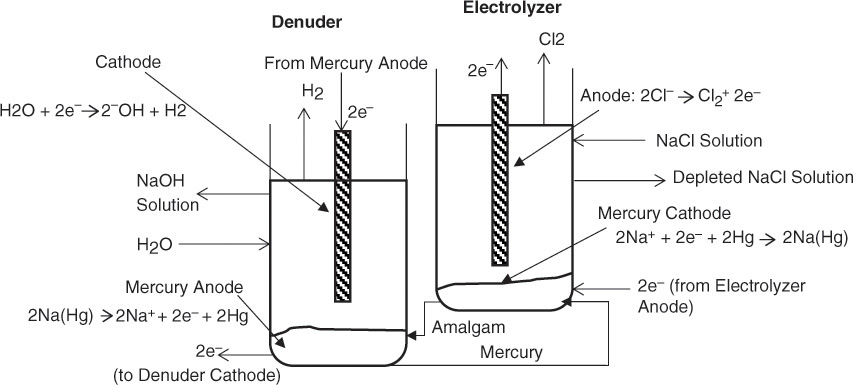
Figure 2.7 Schematic representation of mercury cell used in chloralkali industry.
The oxidation of chlorine in mercury cells is accompanied by the reduction of sodium ion to elemental sodium on a mercury cathode, leading to the formation of sodium amalgam. The amalgam then flows to a denuding chamber where the elemental sodium is oxidized back to sodium ion, with the hydroxide ion formation constituting the reduction reaction. The diaphragm/membrane cells constitute the majority of the electrolyzers, in no small measure due to environmental concerns related to mercury.
Caustic soda is used in a large number of industries, with pulp and paper and organic chemical manufacture accounting for nearly 40% of its use [1]. Other significant applications include soaps and detergents, petroleum refining, water treatment, and textiles. Chlorine, originally considered as a by-product of the electrolysis process because of its limited use, is often now considered the primary product because of its use in the manufacture of organic chemicals. It is used extensively in the intermediate processing steps in organic processes and is frequently not present in the final product. Synthesis of propylene oxide from propylene via chlorohydrin process is a typical example where chlorine is used in the intermediate steps. The largest single use of chlorine is in the synthesis of ethylene dichloride, most of which ends up ultimately as PVC. Other significant uses of chlorine include pulp and paper bleaching, synthesis or manufacture of inorganic compounds, and water treatment.
2.5.3 Nitrogen and Oxygen
Nitrogen is one of the most important chemicals produced in large quantities worldwide, primarily for conversion to ammonia, without which it would be impossible to feed the growing human population. Nitrogen and oxygen are present abundantly in air; however, the process for separating the two and obtaining high-purity products is quite complex. Large-scale production of the two is accomplished by cryogenic distillation of air at temperatures ~83 K (−190°C) [1]. Before the mixture can be subjected to distillation, air needs to be cleaned of impurities that include particulates and other components, such as carbon dioxide, water, trace organics, and others, that make the process quite complicated. Further, a substantial amount of energy needs to be expended in the liquefaction of air, and cooling of the process feed is challenging, particularly because compressing the air for processing generates additional heat. Cooling the air to low temperatures also causes formation of solids—ice and dry ice—that need to be managed and removed properly.
Most of the nitrogen produced is intended for “captive” use; that is, it is produced specifically for manufacturing ammonia [2]. However, there are several other applications of nitrogen, many owing to its nonreactive nature. It provides an inert atmospheric blanket for many processes where the presence of species such as oxygen, water vapor, and others is highly undesirable. Nitrogen is also used for EOR, where it is pumped into oilfield reservoirs to maintain pressure and force oil out for additional recovery.
Pure oxygen, produced along with nitrogen, is valuable for its reactivity. Oxidation is a common process in chemical and other industries, and use of oxygen rather than air has several advantages, including increased efficiencies and higher processing temperatures. Further, significantly lower volumes of gas need to be handled. One of the largest uses of pure oxygen is in the steel industry, where it is used in basic oxygen or open-hearth furnaces. Pure oxygen is also used in the synthesis of ethylene and propylene oxides and in oxyacetylene torches for welding and cutting metals [2].
2.5.4 Hydrogen and Carbon Dioxide
The second element necessary for synthesizing ammonia is hydrogen, by far the most abundant element in the solar system, and on a molar basis, the fourth-most abundant element on earth [7, 8]. However, almost all of this hydrogen is bound in chemical compounds, and molecular hydrogen is obtained from these compounds—hydrocarbons or water. Steam reforming of methane is the dominant production process for hydrogen, accounting for over 48% of the hydrogen produced globally [9]. The fundamental reactions involved in the process are as follows:


The reactants and products of both the reactions are in the gaseous phase. Both the reactions are reversible as well; however, only the desired forward reactions are shown in the equations. The first equation represents the steam-reforming reaction, and practically any hydrocarbon can be subjected to this reaction to obtain hydrogen. The second reaction is called the water-gas shift reaction, which yields additional hydrogen while also converting the carbon monoxide to carbon dioxide. The gas mixture is then separated, typically through a combination of absorption (of carbon dioxide) and membrane separation processes. Figure 2.8 shows a simplified flowsheet for hydrogen production.
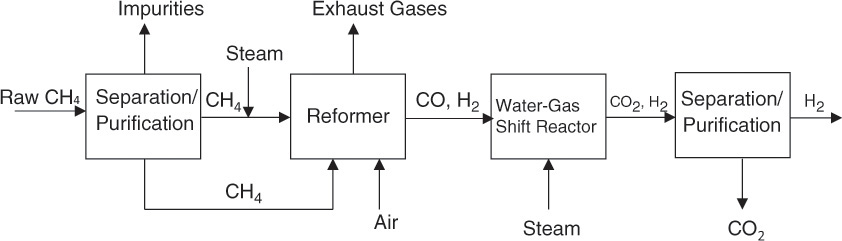
Figure 2.8 Hydrogen production by steam-reforming process.
Methane needed for the reforming reactions is obtained from the natural gas, which is subjected to various separation and purification operations to remove the impurities that include sulfur compound and many others. Similar operations are needed when other hydrocarbons are used as raw materials. The steam-reforming reaction is highly endothermic, and the heat necessary for the reaction is typically obtained by burning a part of methane. The reaction product—the carbon monoxide–hydrogen mixture—is called synthesis gas, or syngas, and is subjected to the water-gas shift reaction, typically conducted in two stages. Both the reforming reaction and the water-gas shift reaction are catalytic reactions. The final stage in the process involves complicated separation and purification steps yielding both hydrogen and carbon dioxide.
Invariably, all the hydrogen produced is for captive consumption—either conversion to ammonia or for upgrading hydrogen content and removing impurities in refinery operations. It is also used in the production of other chemical compounds, such as methanol. Hydrogenation is a common reaction step in many organic syntheses. Synthesis gas, a mixture of carbon monoxide and hydrogen at various ratios, can be used for production of transportation fuels using the Fischer-Tropsch process [2].
As can be seen from the figure, carbon dioxide is a by-product of the steam-reforming process. Large quantities of carbon dioxide are also generated through the combustion of the fossil fuels; however, most of this carbon dioxide is generally emitted to atmosphere. Carbon dioxide is used for EOR as well, but its major use is in refrigeration. Other significant uses involve beverage carbonation, maintenance of inert atmosphere, and chemical manufacture [1].
2.5.5 Ammonia
The manufacturing process for ammonia requires highly pure nitrogen and hydrogen gases, which are produced using the two other significant production processes previously described. Cryogenic distillation of air yields the nitrogen necessary for ammonia synthesis, and the hydrogen required is invariably generated by the steam-reforming of methane (natural gas). Although both these processes, in themselves, represent remarkable manifestation of engineering endeavors, the ammonia synthesis process represents a crowning achievement of chemical engineering. The equation for the gas phase reaction is straightforward:

However, the reaction is reversible; that is, product ammonia tends to decompose back into nitrogen and hydrogen. The reaction must be carried out at high enough temperature to have a reasonable rate of reaction. However, increasing the temperature results in limiting the conversion of reactants or formation of ammonia as the reverse reaction starts to become more favorable. Further, nitrogen and hydrogen will react only slowly in absence of a catalyst, and several eminent scientists and engineers spent considerable time, effort, and money on investigating the reaction until a suitable catalyst—iron with various promoters—was found by Fritz Haber, and further engineering development was conducted by Carl Bosch [10]. A simplified block flowsheet of the process for ammonia synthesis is shown in Figure 2.9. A key point to note in this process is that the product gases exiting the converter are recirculated to the reactor after the recovery of ammonia.
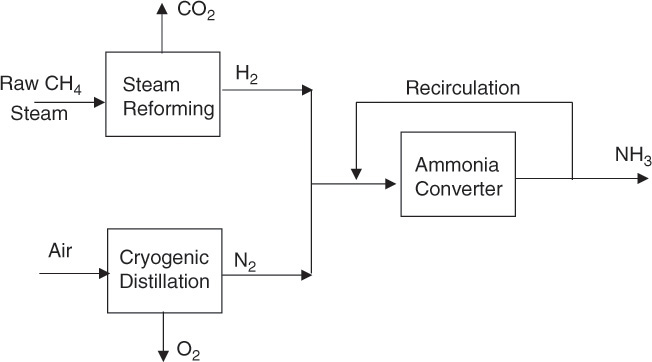
Figure 2.9 Simplified flowsheet of ammonia synthesis process.
As mentioned earlier, the dominant use of ammonia is for making fertilizers: all the N in the fertilizers is ultimately derived from ammonia, through either ammonium ion or nitrate via nitric acid. Ammonia, through nitric acid, also finds applications in explosives. It is also used in the synthesis of polymers, via urea in formaldehyde resins or via various other precursors in nylon.
2.5.6 Soda Ash (Sodium Carbonate)
Soda ash is one of the largest-volume basic inorganic chemicals, as can be seen from Table 2.4. The biggest use of soda ash is in the glass industry, as nearly 90% of all glass is soda-lime-silica glass [1]. Soda ash, due to its alkaline nature, competes with caustic soda in applications that are related to this alkaline nature. These involve soap/detergent and other chemical manufacture as well as the paper and pulp industry. Soda ash, being a milder alkali than caustic soda, may be preferable in applications that do not require strongly alkaline conditions. Caustic soda is preferred for processes requiring a stronger alkali and for the processes where evolution of carbon dioxide cannot be tolerated or is undesirable.
Historically, soda ash was produced by the LeBlanc process, which was replaced by the ammonia-soda or Solvay process. The Solvay process is an elegant example of application of chemical engineering principles, with the main reactions as follows [1]:



The carbon dioxide needed for the reaction is obtained from calcium carbonate decomposition. Calcium oxide formed in the reaction is hydrated to form calcium hydroxide. Ammonium chloride generated in the second reaction, as shown by equation 2.5, is reacted with the calcium hydroxide, generating ammonia needed for the first reaction. Thus, ammonia is completely recycled and not consumed in the process, and the net reaction is between sodium chloride and calcium carbonate as follows:

Despite the elegance and use of inexpensive raw materials, the Solvay process is scarcely used in the United States because huge deposits of sodium sesquicarbonate (Na2CO3·NaHCO3·2H2O) in Wyoming readily yield a material that needs hardly any processing for obtaining the product. Solution mining of the deposits, wherein the material is dissolved underground in situ and the solution is pumped up, has lowered the cost significantly, making the Solvay process uneconomical.
2.5.7 Ethylene and Propylene
As can be seen from Table 2.4, ethylene is by far the largest-volume basic organic chemical produced. Almost all of the ethylene produced worldwide is derived from crude oil, with some obtained from natural gas. Distillation of crude oil results in a number of different fractions ranging from methane to asphalt and coke. In general, the fractions in the order of increasing carbon number are refinery gases (C1–C4 alkanes), gasoline, naphtha, kerosene, diesel, gas oil, fuel oil, lubricants, waxes, and asphalt and coke [2]. Very little of the light fraction is ethylene, which is produced from ethane, propane, naphtha, and other hydrocarbons through a process called cracking. Cracking is a versatile process in refineries whereby molecular bonds in hydrocarbons are cleaved and rearranged to obtain desirable products. Cracking using catalysts, typically in a fluid-bed catalytic cracker, is usually conducted to obtain gasoline [11]. The lighter alkenes, such as ethylene and propylene, are obtained by thermal cracking (also called steam cracking) in absence of a catalyst at ~1600°F [1]. Steam cracking of ethane, propane, liquefied petroleum gas, and naphtha yields ethylene. Propylene is also obtained in the process except when the starting material is ethane.
Nearly all of the ethylene produced ultimately ends up in a polymer—directly in low-density and high-density polyethylenes or indirectly through ethylene oxide to glycol and polyesters, through vinyl chloride to PVC, or through styrene to a number of polymeric products. Similarly, a large fraction of propylene ends up as a polymer, either directly as polypropylene or indirectly through propylene oxide and acrylonitrile. Propylene is also converted to intermediates such as cumene and isopropyl alcohol, which are further processed into other chemical products.
2.5.8 Benzene, Toluene, and Xylenes
Toluene does not appear in Table 2.4 yet is included here with the discussion of benzene and xylenes, as all three are present in the aromatic fraction in petroleum refining. Catalytic reforming of naphtha, the process used for obtaining benzene and xylenes, also yields toluene. While a large percentage of toluene is converted to the more valuable benzene through hydrodealkylation, it finds widespread use as organic solvent and raw material for trinitrotoluene and is also converted to toluene diisocyanate for synthesizing polyurethanes. Benzene, combined with ethylene, forms ethylbenzene, which is dehydrogenated to styrene and ultimately converted into polymers. Benzene hydrogenation yields cyclohexane, a solvent and a precursor for nylon 6 and nylon 66. Other significant chemicals obtained from benzene include cumene and aniline, which are further converted into other chemicals, including polymers. The xylene fraction consists of meta (m-xylene), ortho (o-xylene), and para (p-xylenes), in the order of increasing importance. p-Xylene is the starting material for terephthalic acid and dimethyl terephthalate. Both the acid and the ester are converted into polyesters, PET and PBT, that find applications in fibers, bottles, automotive components, and many others. o-Xylene is generally converted into phthalic anhydride, an intermediate for the synthesis of plasticizers. Most of the m-xylene is generally converted into the other two isomers.
In addition to these chemicals, several other high-volume chemicals can readily be recognized from the trade data. The books Shreve’s Chemical Process Industries [2] and Survey of Industrial Chemistry [1] offer far more comprehensive information about a large number of chemicals and should be the first resources to be consulted for such purposes.
2.6 Characteristics of Chemical Industries
The plants and processes in chemical process industries possess the following major characteristics:
• Large production capacity: The average production capacities of plants engaged in the manufacture of bulk chemicals such as sulfuric acid, ammonia, and ethylene can easily reach into thousands of tons per day (tpd). The largest sulfuric acid plant in the United States has a capacity to produce 4500 tons of acid per day. A plant producing 100 tpd of sulfuric acid is classified as a small plant. The average size of an ethylene unit is about 2500 tpd. Most chemical processes benefit from the economy of scale; that is, the capital and operating costs do not increase linearly with capacity, making larger units more profitable than smaller ones. The large size of the units also means that the industry is highly capital intensive [1].
• Continuous operation: Almost all the plants producing bulk chemicals operate in a continuous, steady-state mode, where conditions are invariant with respect to time. Pharmaceuticals and fine chemicals produced in lower quantities are often produced in batch processes. Even for these plants, while the reaction may be conducted in a batch reactor, the subsequent processing may be carried out in a continuous mode.
• High productivity: A consequence of the continuous operation is the high degree of automation in the chemical processes. Increasingly, the processing steps are controlled and run by computers, requiring minimal operator input. The combination of the economy of scale and high degree of automation has resulted in lower manpower requirements, in turn increasing personnel productivity as measured by metrics such as production volume per plant employee.
• Product diversity: The industry produces practically an unlimited number of products with widely varying characteristics. The products can be gaseous, liquid, or solid; organic or inorganic; volatile or nonvolatile; acidic, basic, or neutral; water soluble or insoluble; biodegradable or persistent; and many other contrasting properties. The applications also show remarkable extremes: from fertilizers and life-saving drugs to pesticides and defoliants, from cosmetics to solvents that dissolve metals and paints, and so on. The outputs of different processes may not share any characteristics, yet the processes can be amenable to analysis and design based on the same fundamental chemical engineering principles.
• Energy consumption and integration: The chemical industry is a major consumer of energy. The Energy Information Administration of the U.S. Department of Energy maintains exhaustive data on all aspects of energy in the United States. According to data from its Manufacturing Energy Consumption Surveys (MECS), the chemical industry accounts for 25% to 30% of the energy consumed by the manufacturing sector. Most chemical processes feature many steps that require energy (heat/electricity) input and many that release thermal energy. Chemical industries seek to manage these energy flows effectively by integrating them across various units.
Chemical industries differ significantly from other manufacturing industries with respect to the following three aspects:
• Uniform product functionality across scale-up and division: The output products of the chemical industries retain their physical and chemical characteristics after physical division, right up to the molecular level. Products of other manufacturing industries lose their defining characteristics and functionality if split into parts. For example, machines, engines, tools, and computers cease to be commercial products if cut into parts. The chemical product stream can be split into many divisions or scaled-down to any level without any loss of characteristics as compared to the parent stream.
• True continuity of operations: The continuous processes in chemical industries operate in a truly continuous manner, that is, with infinite frequency of product formation, or no interruption in the output stream. Several other manufacturing industries may also operate continuously around the clock—24 hours a day, 365 days a year (except for maintenance). However, the output is invariably in the form of discrete objects that are produced at some frequency with a time-interval between output units.
• Uniformity of product properties and uses: The characteristics of a chemical product are essentially independent of the manufacturer and the manufacturing process. For example, acetic acid produced by methanol carbonylation is virtually indistinguishable from that produced by ethylene oxidation. Whether produced by BP Chemicals or Millennium Chemicals, its properties and applications are practically identical. Products of other manufacturing industries retain their identity (manufacturer, model, etc.) and differ to a much greater degree across different manufacturers.
Chemical and allied industries are a mosaic of industries with products that bear no resemblance with each other and yet share many unifying characteristics. With its global reach, the chemical industry offers an opportunity for an engineer in practically any place in the world. The American Chemical Council (ACC, www.americanchemistry.com), a trade association of companies engaged in the chemical business, estimates that the business of chemistry supports 25% of the U.S. gross domestic product. Figure 2.10 shows the growth in the chemical business over the past 6 years, with its 2015 contribution being $801 billion, reflecting an average annual growth rate of ~2.5% since 2010. According to the ACC, each job in the chemical sector generated nearly 6.3 other jobs in the economy [12].
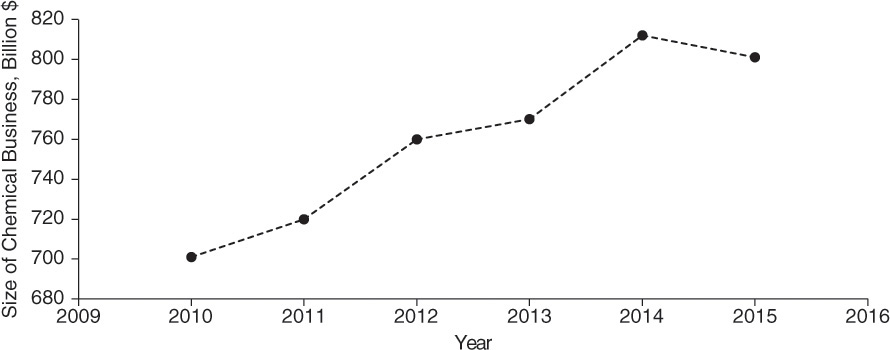
Figure 2.10 Growth of chemical business from 2010 to 2015.
Even the briefest of introduction to just a few of the tens of thousands of chemical products and the chemical processes for manufacture should make clear the wide variety of challenges faced by a chemical engineer. The education of a chemical engineer must prepare him/her to deal with any type of reaction or separation and handle any chemical while contributing to the profitability of the enterprise within the legal, ethical, and moral constraints placed by the society. How this is accomplished by the chemical engineering programs is described in the next chapter.
Leave a Reply