The course listed most often as Chemical Reaction Engineering or Chemical Engineering Kinetics explains and teaches the design of chemical reactors. The essence of the design problem is explained simply as follows: It is desired to produce a certain quantity of a chemical determined by the market demand for that chemical. The engineer is required to specify the size of the vessel and the operating conditions for producing the chemical at the desired rate.
To solve this design problem, the engineer needs to understand the factors governing the rate of the reaction, which is generally defined in terms of the quantity reacting per unit time per unit measure of reactor size. The intrinsic kinetics of the reaction is dependent on the concentrations of species involved in the reaction as well as the temperature. Additional factors that play a role in determining the actual or observed rate in the reactor may include flow rate and pattern, agitation speed, and so on.
The course on reactor and reaction engineering teaches students the fundamental concepts and techniques related to reactor design. The desired outcome of the course is competency on the part of the student in design and analysis of chemical reactors for the different types of reactors employed in chemical processes. Following are some of the core concepts taught in the course:
• Determination of intrinsic kinetics: The student learns about quantifying the rate of reaction and factors determining this rate. The parameters in the rate expression (equation representing the relationship between the rate and factors affecting the rate) need to be determined experimentally, and the student learns about conducting laboratory experiments for this purpose, as well as analysis and interpretation of the data obtained.
• Design of reactors: The types of reactors used in the chemical industry can be categorized on the basis of a number of different criteria: whether they are operated in a batch mode, where conditions change with time, or in a continuous mode, where conditions are invariant and the system is at a steady state; whether the reactors operate under isothermal (constant temperature) or nonisothermal (temperature varying with time or position within the reactor) conditions; whether the reaction is homogeneous (single phase) or heterogeneous (two or more phases); and so on. Figure 3.3 shows the schematic sketches of batch and continuous reactors used in the chemical industry [7]. The operational characteristics of batch and continuous reactors are qualitatively and quantitatively different from each other. Design of batch reactors involves determining the batch size and time, whereas the design of continuous reactors involves determining the reactor size or residence time. Continuous reactors are further classified according to the flow pattern. Design equations for mixed flow reactors (contents well mixed) are different from segregated flow reactors (contents not intermixed). A large number of industrial reactions are fluid-solid heterogeneous reactions, the solid being a catalyst. Many other reactions involving a solid phase are noncatalytic; that is, the solid participates in the reaction. Each of these cases requires a distinct approach for reactor design, which a chemical engineering student must understand and master.
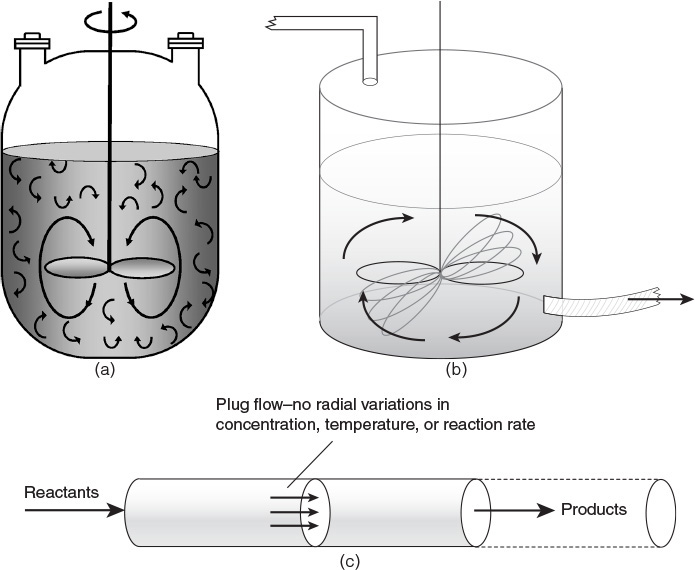
Figure 3.3 Batch and continuous reactors—(a) batch reactor, (b) continuous stirred tank reactor, (c) tubular plug flow reactor.
Source: Fogler, F. S., Elements of Chemical Reaction Engineering, Fourth Edition, Prentice Hall, Upper Saddle River, New Jersey, 2004.
• Analysis of flow characteristics: The mixed flow reactor and the segregated flow reactor represent ideal flow reactors. The actual flow pattern in operating reactors frequently does not conform to the idealized flow pattern. A student must learn to model the flow pattern and develop analytical techniques to identify the departure from ideality for accurately predicting the extent of reaction and implementing corrective measures.
The generalized concepts learned in this course enable a chemical engineer to apply the knowledge for any reactor system ranging from a single homogeneous reaction to multiple reactions in complex systems, such as enzyme-mediated reactions of complex substances in biological systems.
Leave a Reply